20HL Auto 5 Vessel Brewhouse in Russia
- Jul 12, 2024
- 150
- tiantai
Russia is a relative late-comer as a beer nation, but as of 2010 it had come to rank as the world’s fourth-largest beer market, after China, the United States, and Brazil. Beer, pivo in Russian, is the second most popular alcoholic beverage, after vodka, and it is generally preferred to wine. Russian beers are mainly lagers, and pale lagers are the most common. In Russia, beer is categorized by color, not by style, or the yeast that ferments it. Beer is therefore looked upon as simply light, red, semi-dark, or dark. Russians purchase beer mostly in cans and PET bottles, and less frequently in glass bottles.
Have you ever considering to start a brewery to start your beer business? Here are some basic factors we need to consider before choosing the perfect size and capacity for your brewing equipment.
1) Production Volume. ...
2) Available Space. ...
3) Brewing Process and Batch Sizes. ...
4) Scalability and Growth. ...
5) Budget and Financial Considerations. ...
6) Utility Requirements. ...
7) Equipment Integration and Compatibility. ...
8) Supplier Reputation and Support.
We had installed a 20HL 5 vessel brewery in Russia, the basic configurations as below:
1) PLC control + pneumatic valves + various sensors
2) Auto water mixing + auto wort cooling + auto wort lautering
3) Spent grain auto discharge + grain rake auto lifted
4) Pneumatic valve above hydrator for auto feeding
5) Auto CIP station + auto injection unit
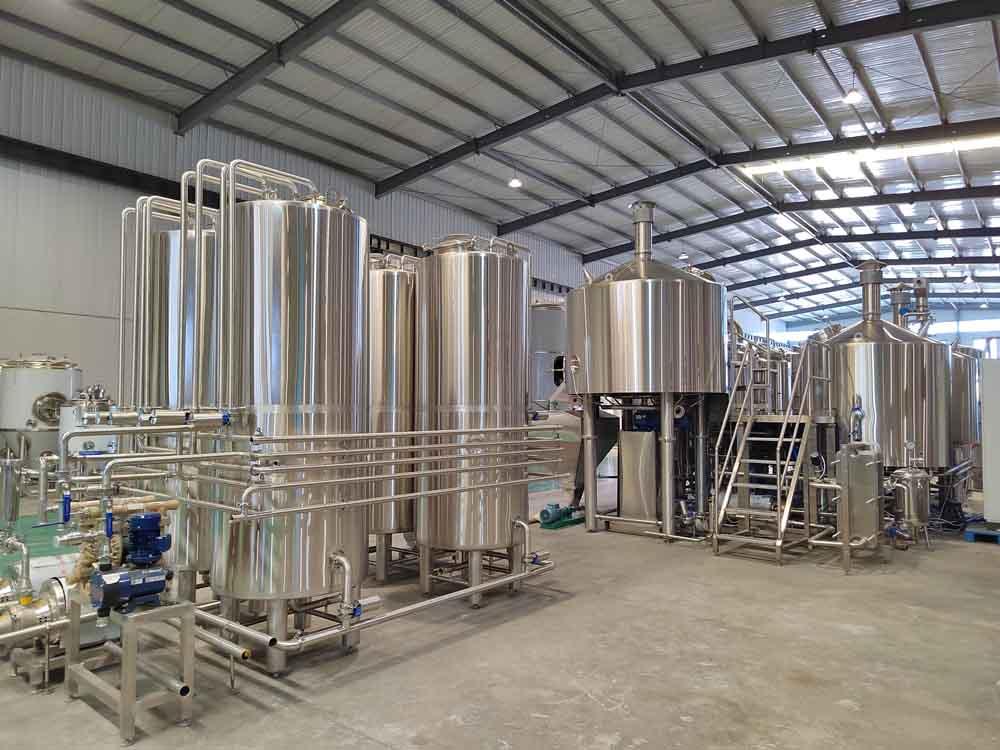
The brewing system automation level is higher, automated brewing systems can help brewers save time and money while ensuring the consistent quality of their products. Automatic brewing systems save a lot of labor in the brewing process. They can perform many tasks such as mashing, boiling, fermenting, and conditioning beer without any human intervention.
With an automated brewing systems simplify the brewing process a lot.
Recipe accuracy
Automation brings a level of precision to the brewing process, ensuring consistency from batch to batch. From malt grinding to hop addition, automated systems follow recipes to the letter, reducing human error and increasing the ability to replicate desired flavor profiles.
Improved brew control
Automation provides brewers with precise control over key brewing parameters. Temperature, pressure, and flow rate can be adjusted for more predictable and repeatable results. This level of control is particularly beneficial during the mashing, filtering, and boiling processes, where slight deviations can affect the final product.
Strengthen fermentation monitoring
Fermentation is a collision between yeast and wort, and maintaining optimal conditions is crucial. Automated fermentation monitoring systems allow breweries to track temperature, gravity, and other parameters. This real-time data enables brewers to make informed decisions to produce high-quality beer.
Precise temperature control
Temperature plays a vital role in the brewing process. The automated system is equipped with sensors that watch and regulate temperatures to maintain an optimal environment for fermentation and other brewing stages.
Improve production capacity
One of the main benefits of automated brewing systems is increased production capacity. These systems are designed to handle large volumes of beer, allowing breweries to meet growing customer demand. With automated brewing systems, breweries can scale up production without sacrificing quality or efficiency.
The brewing process in an automated system is often automated, which allows for more efficient use of time and increases throughput. These systems often include features such as temperature control, automatic ingredient addition, and monitoring capabilities. By automating every aspect of the brewing process, breweries can increase production capacity while maintaining consistency and quality.
Improve cleaning and hygiene efficiency
Maintaining a clean and sanitary brewing environment is critical to producing contamination-free, odor-free beer. Automated clean-in-place (CIP) systems streamline the process and reduce downtime between batches. Brewers can divide more time to brewing, spend less time cleaning , and increase production efficiency.
Quality assurance
Ensure quality and reduce errors. As automated systems control key aspects of the brewing process such as temperature and time, parameters such as temperature, pH, and pressure are measured. Breweries can track these measurements in real-time and make adjustments as needed to ensure the beer is brewed to the desired specifications. This minimizes the chance of errors that could lead to batch damage.
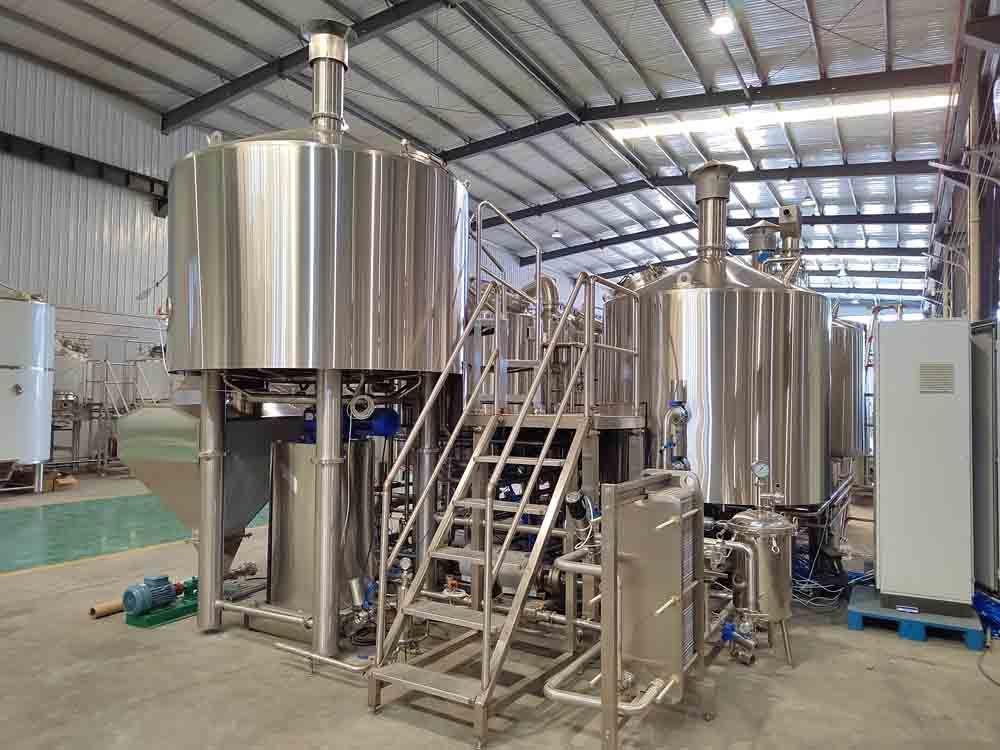
If you are planning to open a brewery. TIANTAI BrewTech could help you answer your questions and supply the brewery equipment system. We supply 2-150bbl complete beer brewing brewery equipment system including malt milling equipment, brewhouse equipment, fermenters, brite beer tanks, beer bottling machine,beer canning machine, beer kegging machine, hopping machine, yeast propagation equipment. We also supply all auxiliary brewery systems like steam heating pipe and valves, water treatment, filter, air compressor etc. Everything in brewery are all in our list. Feel free contact Derrick to get your brewery proposal.
Derrick
Sales Manager
[email protected]
Tiantai Beer Equipment
Have you ever considering to start a brewery to start your beer business? Here are some basic factors we need to consider before choosing the perfect size and capacity for your brewing equipment.
1) Production Volume. ...
2) Available Space. ...
3) Brewing Process and Batch Sizes. ...
4) Scalability and Growth. ...
5) Budget and Financial Considerations. ...
6) Utility Requirements. ...
7) Equipment Integration and Compatibility. ...
8) Supplier Reputation and Support.
We had installed a 20HL 5 vessel brewery in Russia, the basic configurations as below:
1) PLC control + pneumatic valves + various sensors
2) Auto water mixing + auto wort cooling + auto wort lautering
3) Spent grain auto discharge + grain rake auto lifted
4) Pneumatic valve above hydrator for auto feeding
5) Auto CIP station + auto injection unit
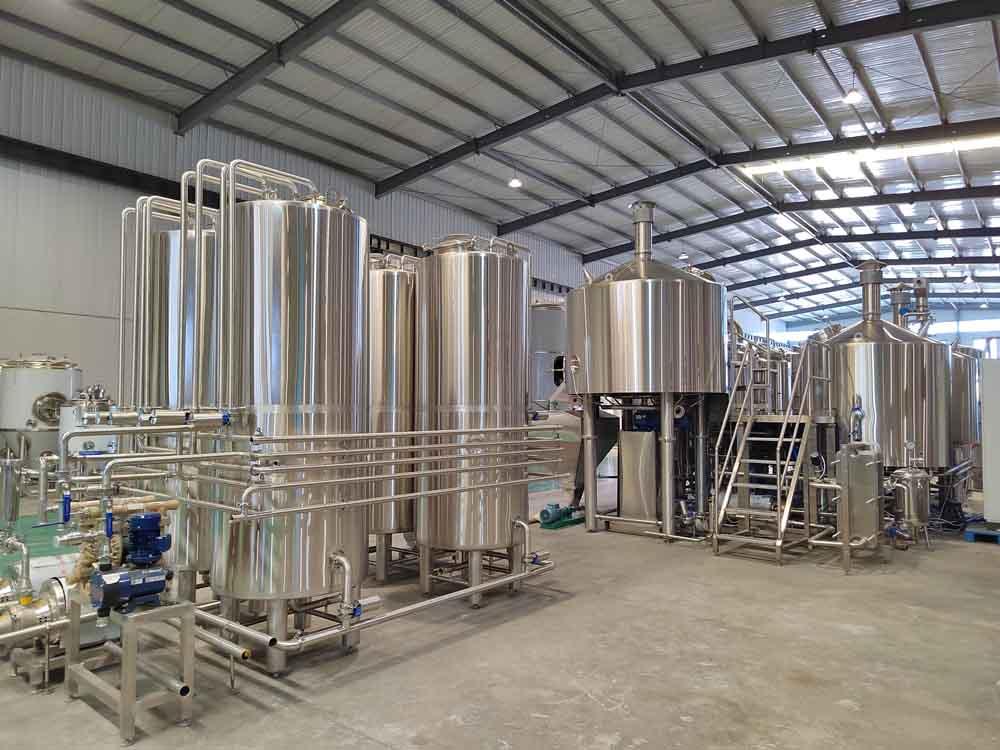
The brewing system automation level is higher, automated brewing systems can help brewers save time and money while ensuring the consistent quality of their products. Automatic brewing systems save a lot of labor in the brewing process. They can perform many tasks such as mashing, boiling, fermenting, and conditioning beer without any human intervention.
With an automated brewing systems simplify the brewing process a lot.
Recipe accuracy
Automation brings a level of precision to the brewing process, ensuring consistency from batch to batch. From malt grinding to hop addition, automated systems follow recipes to the letter, reducing human error and increasing the ability to replicate desired flavor profiles.
Improved brew control
Automation provides brewers with precise control over key brewing parameters. Temperature, pressure, and flow rate can be adjusted for more predictable and repeatable results. This level of control is particularly beneficial during the mashing, filtering, and boiling processes, where slight deviations can affect the final product.
Strengthen fermentation monitoring
Fermentation is a collision between yeast and wort, and maintaining optimal conditions is crucial. Automated fermentation monitoring systems allow breweries to track temperature, gravity, and other parameters. This real-time data enables brewers to make informed decisions to produce high-quality beer.
Precise temperature control
Temperature plays a vital role in the brewing process. The automated system is equipped with sensors that watch and regulate temperatures to maintain an optimal environment for fermentation and other brewing stages.
Improve production capacity
One of the main benefits of automated brewing systems is increased production capacity. These systems are designed to handle large volumes of beer, allowing breweries to meet growing customer demand. With automated brewing systems, breweries can scale up production without sacrificing quality or efficiency.
The brewing process in an automated system is often automated, which allows for more efficient use of time and increases throughput. These systems often include features such as temperature control, automatic ingredient addition, and monitoring capabilities. By automating every aspect of the brewing process, breweries can increase production capacity while maintaining consistency and quality.
Improve cleaning and hygiene efficiency
Maintaining a clean and sanitary brewing environment is critical to producing contamination-free, odor-free beer. Automated clean-in-place (CIP) systems streamline the process and reduce downtime between batches. Brewers can divide more time to brewing, spend less time cleaning , and increase production efficiency.
Quality assurance
Ensure quality and reduce errors. As automated systems control key aspects of the brewing process such as temperature and time, parameters such as temperature, pH, and pressure are measured. Breweries can track these measurements in real-time and make adjustments as needed to ensure the beer is brewed to the desired specifications. This minimizes the chance of errors that could lead to batch damage.
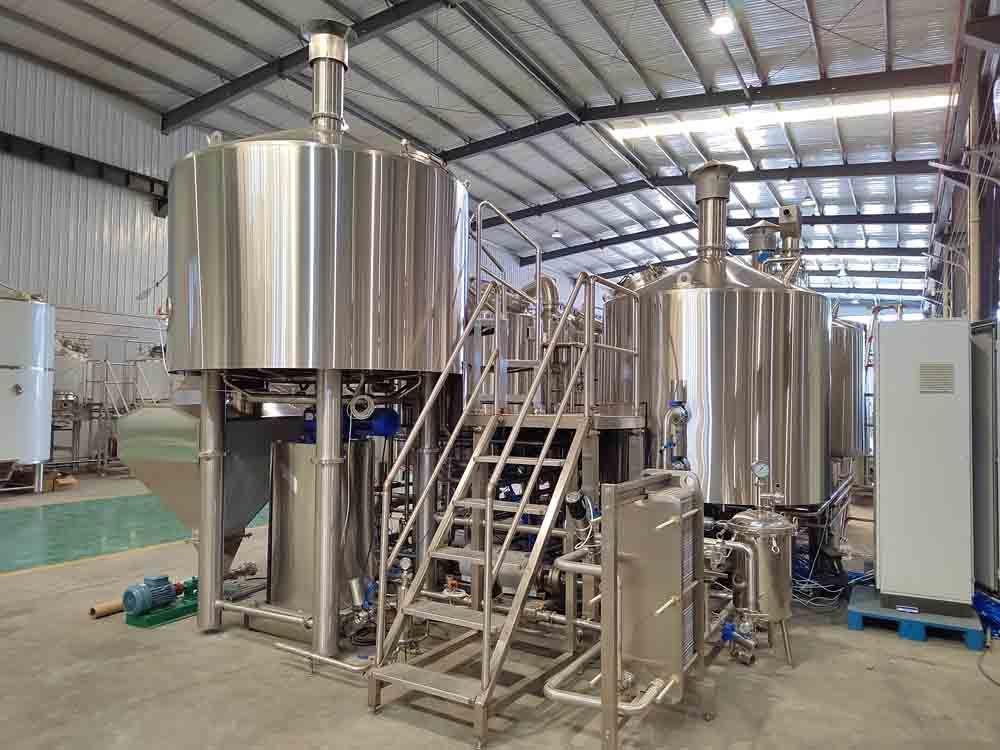
If you are planning to open a brewery. TIANTAI BrewTech could help you answer your questions and supply the brewery equipment system. We supply 2-150bbl complete beer brewing brewery equipment system including malt milling equipment, brewhouse equipment, fermenters, brite beer tanks, beer bottling machine,beer canning machine, beer kegging machine, hopping machine, yeast propagation equipment. We also supply all auxiliary brewery systems like steam heating pipe and valves, water treatment, filter, air compressor etc. Everything in brewery are all in our list. Feel free contact Derrick to get your brewery proposal.
Derrick
Sales Manager
[email protected]
Tiantai Beer Equipment