Optimizing Brewery Equipment Layout in a Multi-Level Brewery
- Apr 02, 2025
- 70
- tiantai
When designing a brewery across two floors, careful planning of equipment placement is crucial for efficiency, safety, and operational convenience. By strategically distributing brewing equipment between the first and second floors, breweries can maximize space utilization, improve workflow, and enhance energy efficiency.
Option 1: Brewhouse on the Second Floor, Fermentation on the First Floor (Recommended)
Best for: Gravity-assisted brewing, reducing energy consumption, and optimizing production efficiency.
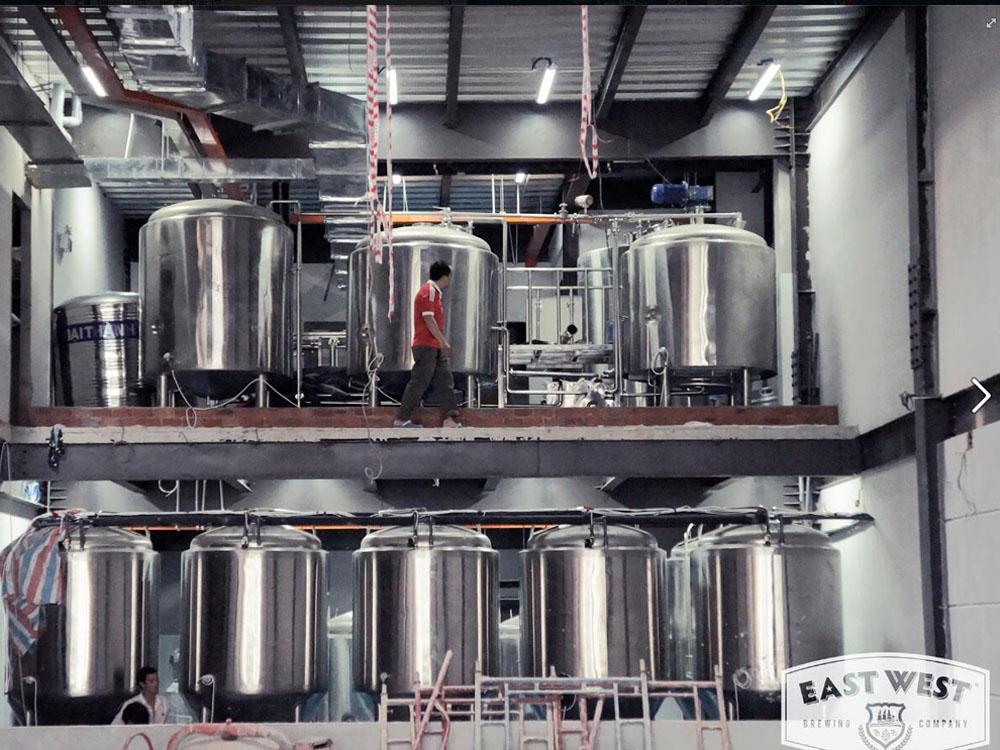
Second Floor (Brewhouse System)
1.) Brewhouse Equipment
* Includes the mash tun, lauter tun, kettle, and whirlpool.
* Allows gravity-fed transfer of wort directly to fermentation tanks on the first floor, minimizing the need for pumps and reducing oxidation risks.
* Raw material storage (such as malt silos and milling equipment) can also be located on the second floor for direct feeding into the mash tun.
2.) Brewhouse Control Room
* Positioned for convenient monitoring and management of the brewing process.
First Floor (Fermentation & Packaging Area)
1.) Fermentation Tanks (FVs)
* Located on the first floor to accommodate their significant weight and ensure structural stability.
* Easily integrates with glycol cooling systems and facilitates efficient temperature control.
2.) Brite Beer Tanks (BBTs)
* Positioned close to fermentation tanks for efficient beer transfer.
* Ensures a streamlined workflow towards packaging and distribution.
3.) Packaging Area
* Includes bottling, canning, and kegging lines, reducing movement and oxidation risks.
* Positioned for direct access to cold storage and distribution areas.
4.) Cooling Equipment (Glycol Chiller)
* Located on the first floor for better integration with fermentation tanks and to reduce heat exposure.
Option 2: Brewhouse on the First Floor, Fermentation on the Second Floor
Best for: Breweries with strong building support and effective pumping systems.
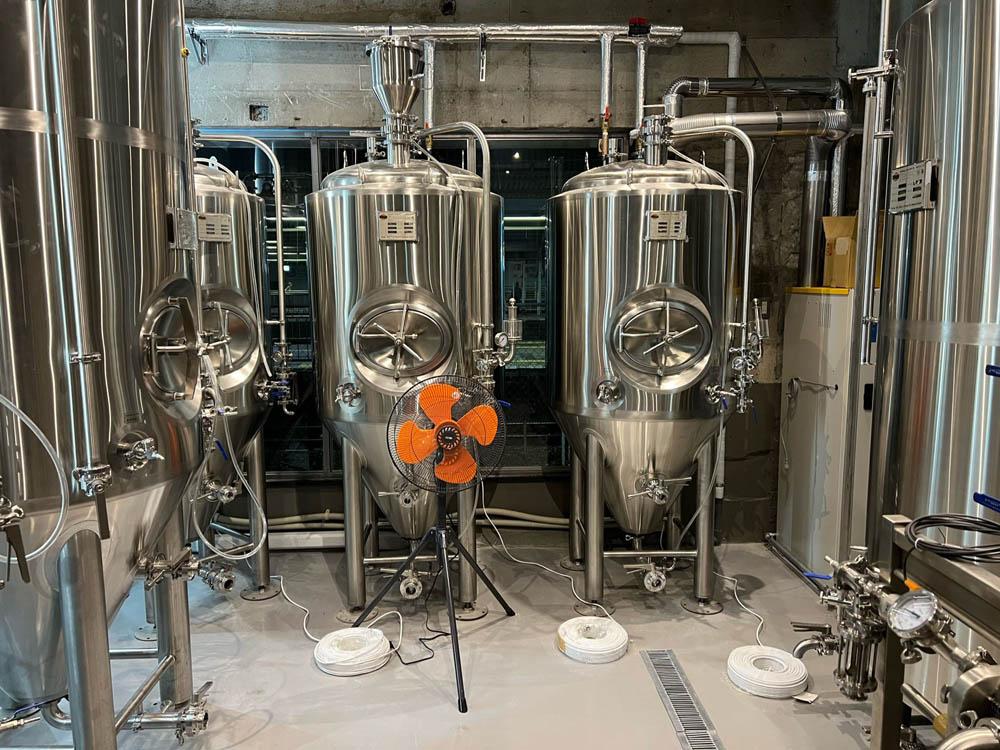
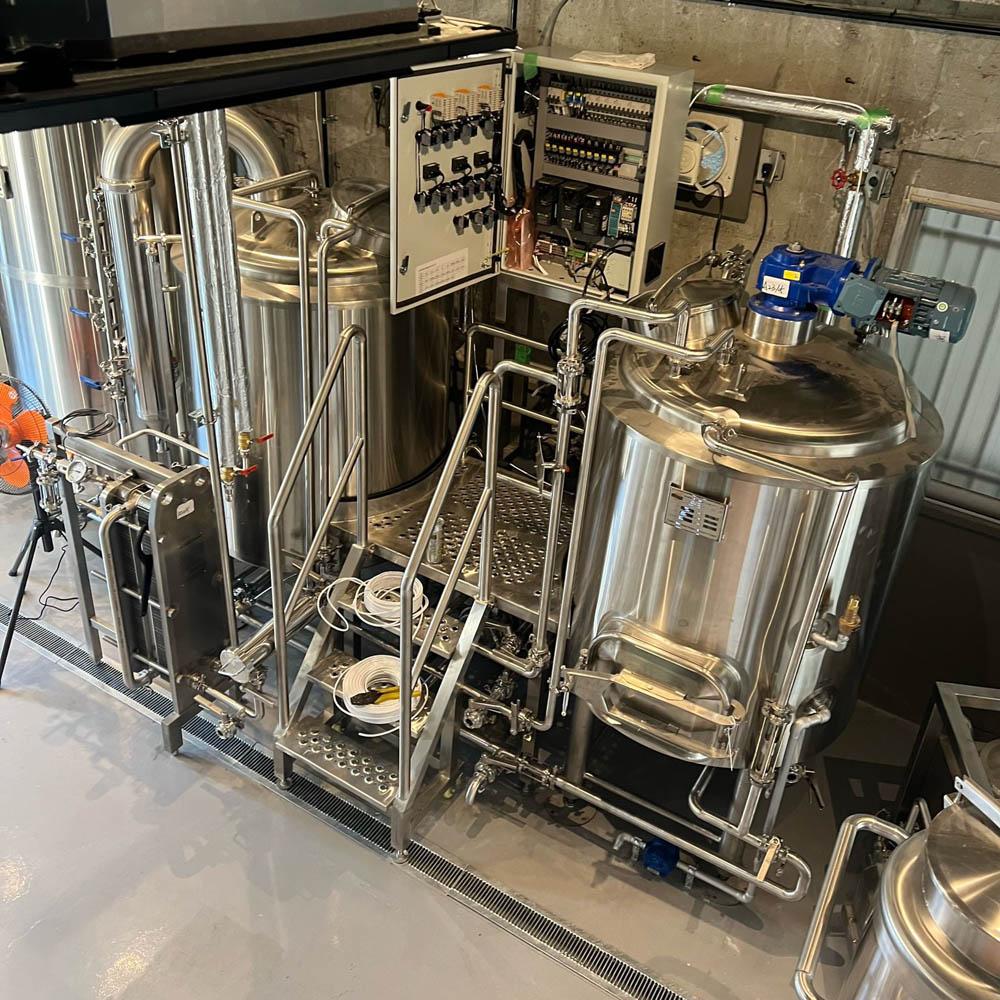
First Floor (Brewhouse System)
1.) Brewhouse Equipment
* Mash tun, lauter tun, kettle, and whirlpool placed on the first floor.
* Wort must be pumped to fermentation tanks on the second floor, increasing operational complexity and energy use.
* Drainage and cleaning processes are more straightforward.
2.) Raw Material Storage & Milling
* Positioned on the first floor for easy access and processing.
Second Floor (Fermentation & Cooling System)
1.) Fermentation Tanks
* Requires structural reinforcement due to the significant weight of filled tanks.
* Must account for ceiling height limitations.
2.) Brite Beer Tanks & Cooling Systems
* Packaging and storage must also be placed on the second floor if BBTs are located there, which can complicate logistics.
Comparing the Two Layouts
Final Recommendation
If structural conditions allow, the preferred layout is placing the brewhouse on the second floor and fermentation on the first floor. This maximizes efficiency, reduces energy use, and ensures a smoother production process.
If fermentation must be on the second floor, additional structural reinforcements and efficient pumping solutions will be necessary.
Are you planning a multi-level brewery? Our team can help you design the optimal layout for efficiency and scalability. Contact us today to learn more!
Edited by Vicky
Sales Director in Tiantai Brewtech
Email: [email protected]
Option 1: Brewhouse on the Second Floor, Fermentation on the First Floor (Recommended)
Best for: Gravity-assisted brewing, reducing energy consumption, and optimizing production efficiency.
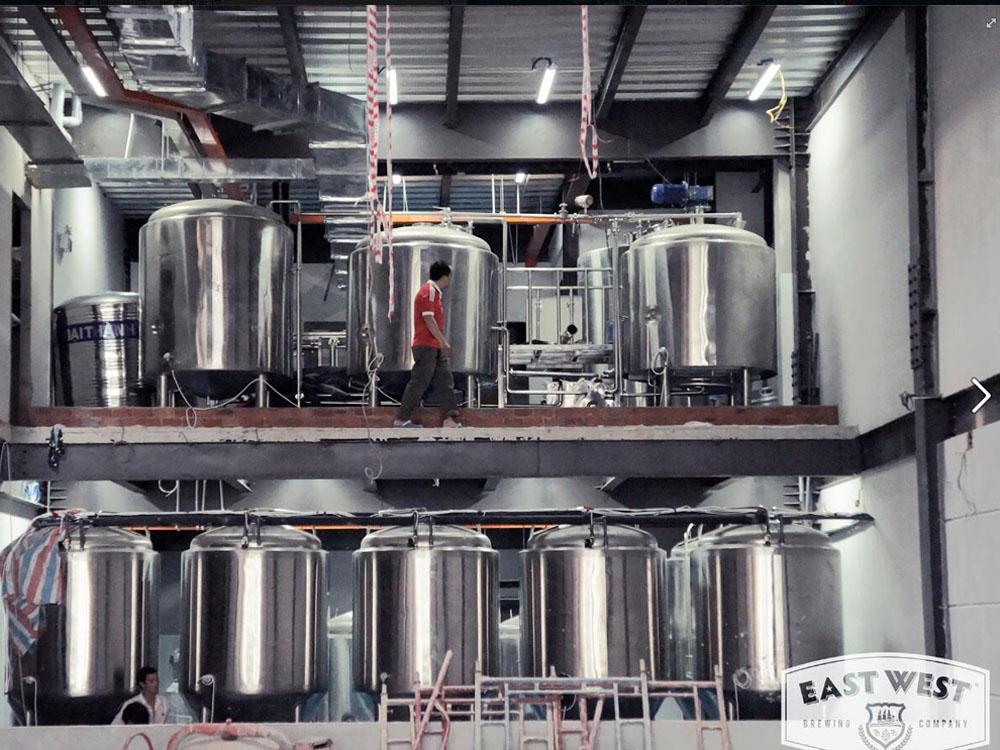
Second Floor (Brewhouse System)
1.) Brewhouse Equipment
* Includes the mash tun, lauter tun, kettle, and whirlpool.
* Allows gravity-fed transfer of wort directly to fermentation tanks on the first floor, minimizing the need for pumps and reducing oxidation risks.
* Raw material storage (such as malt silos and milling equipment) can also be located on the second floor for direct feeding into the mash tun.
2.) Brewhouse Control Room
* Positioned for convenient monitoring and management of the brewing process.
First Floor (Fermentation & Packaging Area)
1.) Fermentation Tanks (FVs)
* Located on the first floor to accommodate their significant weight and ensure structural stability.
* Easily integrates with glycol cooling systems and facilitates efficient temperature control.
2.) Brite Beer Tanks (BBTs)
* Positioned close to fermentation tanks for efficient beer transfer.
* Ensures a streamlined workflow towards packaging and distribution.
3.) Packaging Area
* Includes bottling, canning, and kegging lines, reducing movement and oxidation risks.
* Positioned for direct access to cold storage and distribution areas.
4.) Cooling Equipment (Glycol Chiller)
* Located on the first floor for better integration with fermentation tanks and to reduce heat exposure.
Option 2: Brewhouse on the First Floor, Fermentation on the Second Floor
Best for: Breweries with strong building support and effective pumping systems.
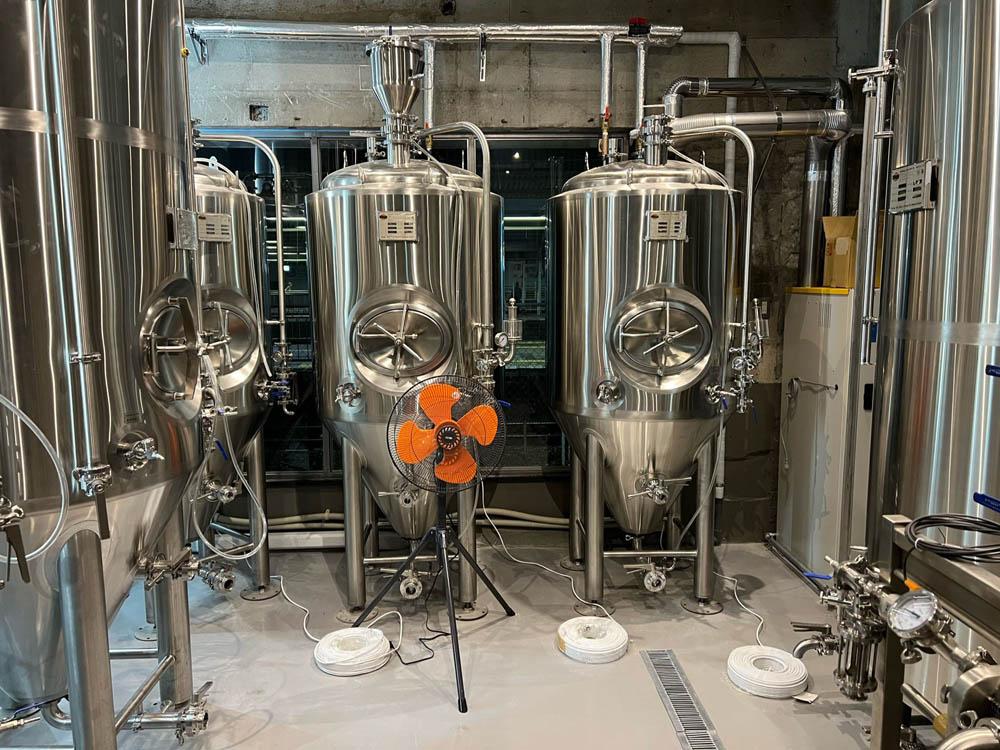
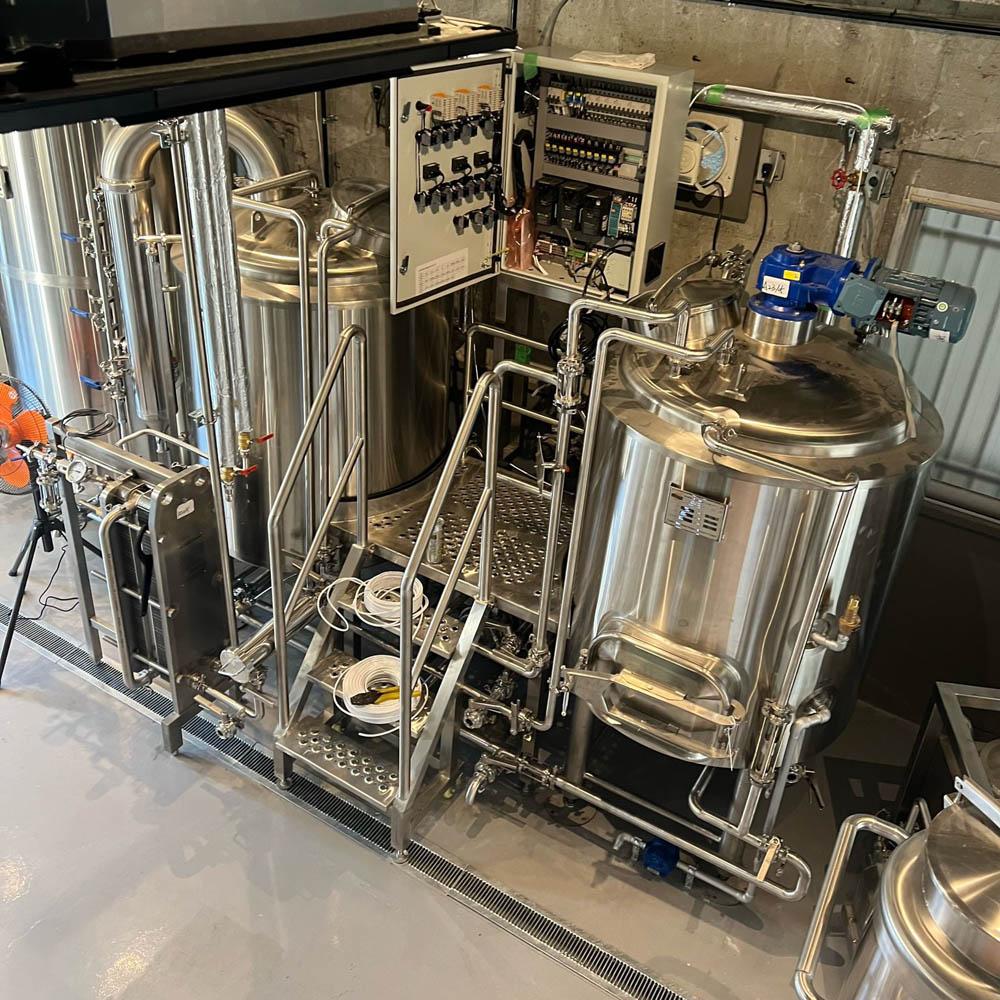
First Floor (Brewhouse System)
1.) Brewhouse Equipment
* Mash tun, lauter tun, kettle, and whirlpool placed on the first floor.
* Wort must be pumped to fermentation tanks on the second floor, increasing operational complexity and energy use.
* Drainage and cleaning processes are more straightforward.
2.) Raw Material Storage & Milling
* Positioned on the first floor for easy access and processing.
Second Floor (Fermentation & Cooling System)
1.) Fermentation Tanks
* Requires structural reinforcement due to the significant weight of filled tanks.
* Must account for ceiling height limitations.
2.) Brite Beer Tanks & Cooling Systems
* Packaging and storage must also be placed on the second floor if BBTs are located there, which can complicate logistics.
Comparing the Two Layouts
Layout | Advantages | Disadvantages |
Option 1: Brewhouse on Second Floor, Fermentation on First Floor (Recommended) |
- Utilizes gravity for wort transfer, reducing energy consumption. - Fermentation tanks remain on the stable ground floor. - Packaging and storage are optimized for distribution. |
- Requires sufficient structural support for brewhouse equipment on the second floor. - Drainage from the second-floor brewhouse must be managed. |
Option 2: Brewhouse on First Floor, Fermentation on Second Floor |
- Easier maintenance of brewhouse equipment. - Reduces humidity concerns on the second floor. |
- Requires pumps to transfer wort upstairs, increasing costs. - Fermentation tanks add structural load to the second floor. |
Final Recommendation
If structural conditions allow, the preferred layout is placing the brewhouse on the second floor and fermentation on the first floor. This maximizes efficiency, reduces energy use, and ensures a smoother production process.
If fermentation must be on the second floor, additional structural reinforcements and efficient pumping solutions will be necessary.
Are you planning a multi-level brewery? Our team can help you design the optimal layout for efficiency and scalability. Contact us today to learn more!
Edited by Vicky
Sales Director in Tiantai Brewtech
Email: [email protected]